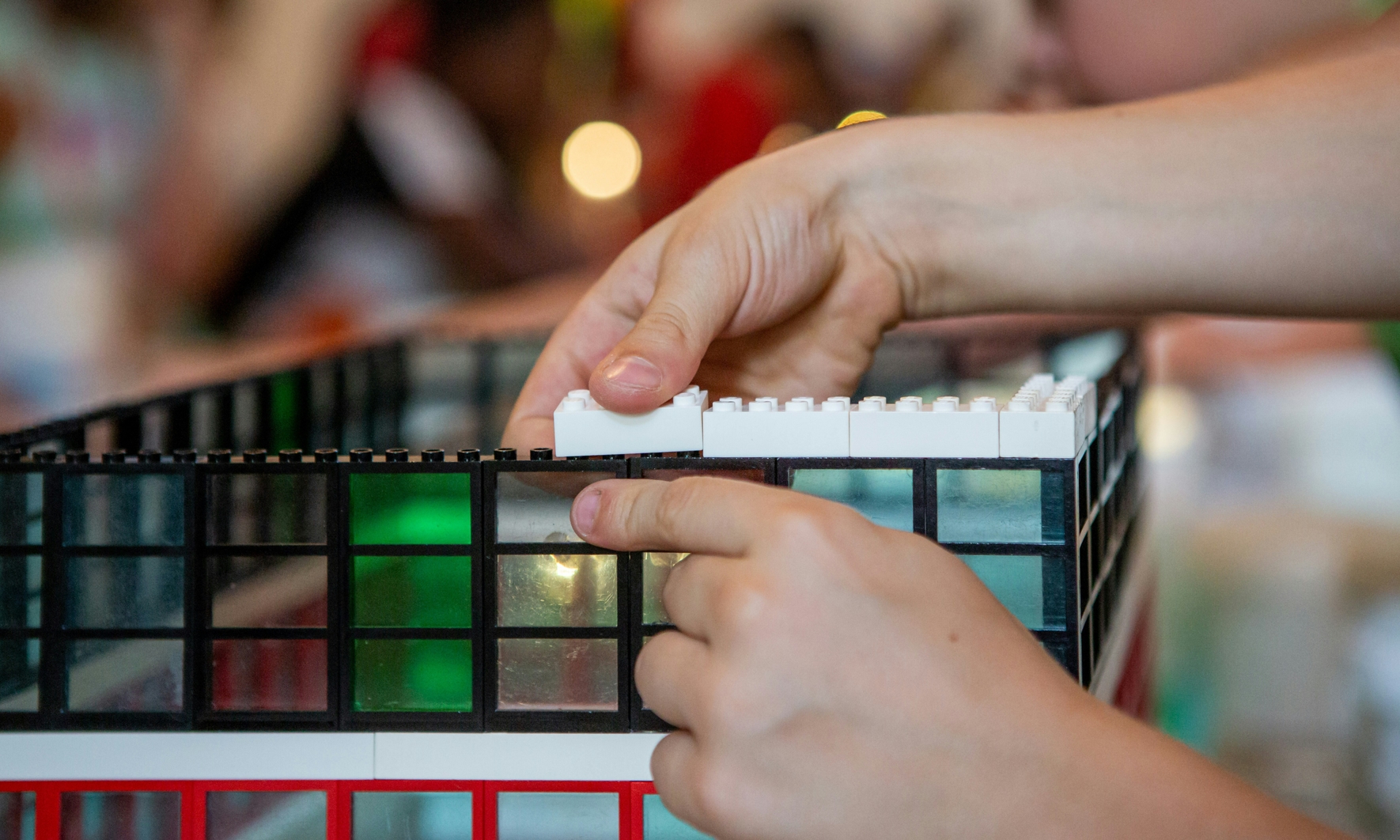
A Uniform “Lego” Approach Saves Costs in Rental Housing Construction— and Creates More Affordable Rental Units
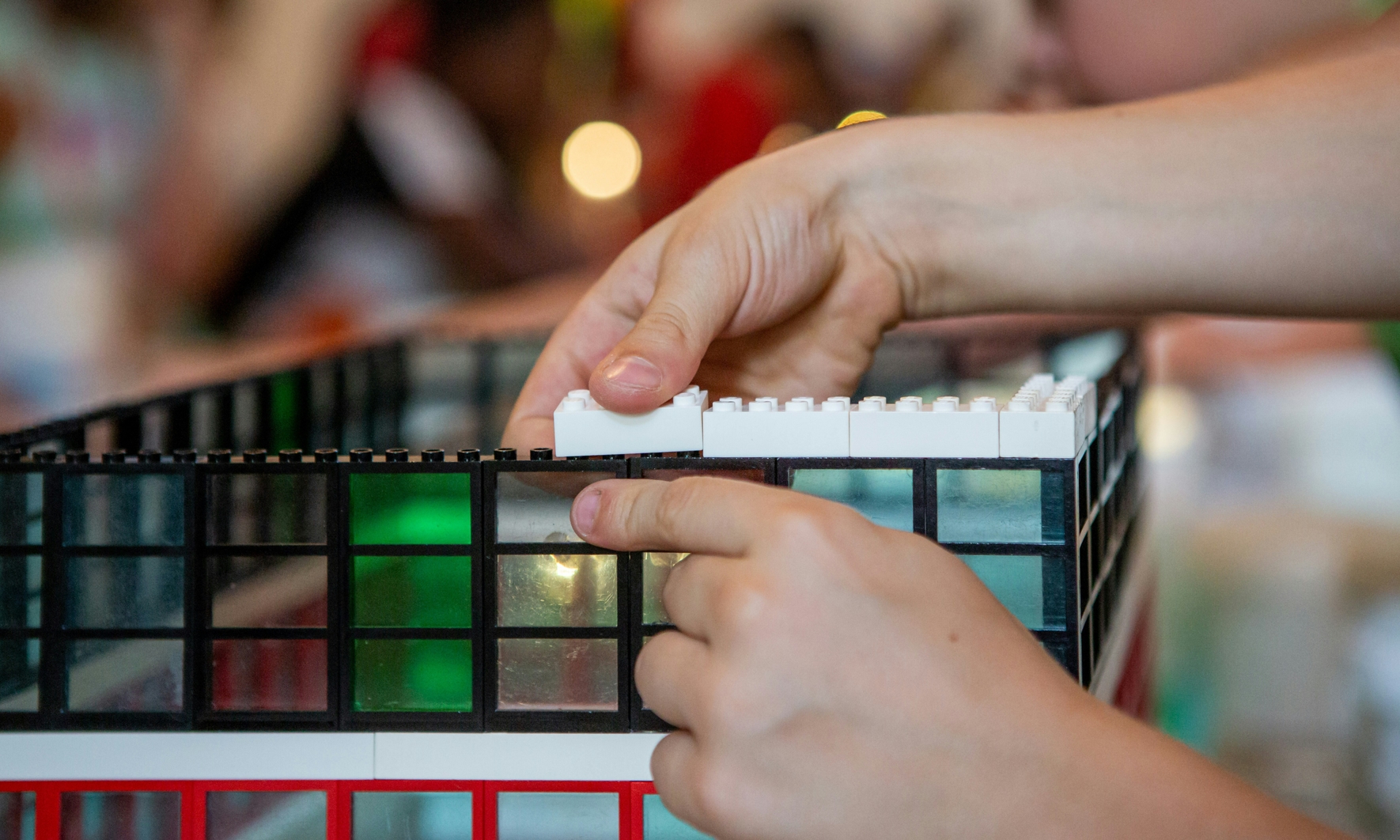
A Uniform “Lego” Approach Saves Costs in Rental Housing Construction— and Creates More Affordable Rental Units
It’s a new age of standardization in the development of multifamily and single-family rental properties
Creating “core” elements of a unit’s interior configuration that can be used again and again, from property to property, thereby creating cost efficiencies—and an end product with more affordability.
This design core typically revolves around the main living area being standardized, i.e. the configuration of the entryway, kitchen, living room, master bedroom and bath, and laundry area. “It’s almost like a lego set,” said Garret Askew, DLP Capital’s Managing Director of Construction. “We can drop a standard configuration into our development designs, and then personalize the surrounding structure.”
Askew estimates that 55%-60% of multifamily developments aimed at middle-market rental properties, including workforce housing, follow core standardization approaches. Single-family rental communities have adopted building templates as well. The approaches to uniformity—and savings—can vary. It may include “panelization” that involves two-dimensional walls built in a factory for jobsite assembly to get the core started and then range all the way up to complete off-site modular unit construction that is then brought on-site to form a building. While the core of a unit may be standardized, the number of additional bedrooms and baths surrounding the core can be tailored to the end user.

How does this core standardization approach save costs? Supply chains can be more controlled. Developers/contractors can better negotiate bulk agreements with national suppliers, for example, since there are more construction “knowns” and fewer variables. This allows a developer to control the quantities, timing, and prices on everything from housing fixtures, finishes, and flooring, to HVAC. There’s also less field cutting, saving labor time and costs.
There is also increased precision with uniformity, which translates into less material use and waste. Take floor trusses—the structural framework between floors (a triangular web configuration similar in concept to roof trusses). Standardized pre-manufactured trusses can be strategically designed to withstand more flex. That precision, in turn, can allow the trusses’ depth to be reduced from 18 inches to 16 inches. Multiply that by three levels, and it saves 6 inches of building height—and related savings from lumber costs to siding and more. Nothing changes in regards to ceiling heights, so residents notice no difference.
Overall, when seeking to minimize costs to create quality, attainably priced rental housing, these types of standardization savings can add up. McKinsey & Company, for example, estimates that modular systems can cut costs by as much as 20%—and speed up construction timetables considerably as well. In addition to the economies of scale, such construction has a green impact, allowing for the use of recycled materials.
Are there downsides to a uniform approach? “It’s important to make sure every development benefits from its own unique character,” added Askew. He points to the wide variety of techniques for giving each development visual distinctions and a unique identity. Distinctions can range from lap siding or board and batten siding, to bump outs, gables, shed roofs, variety in roof pitches, external color schemes, and much more.
In short, standardizing core elements allows for high-quality and precision construction while improving upon costs. By leveraging such uniformity, middle-market developers can create more competitive rental housing—priced to meet the growing housing demands of America’s workforces.